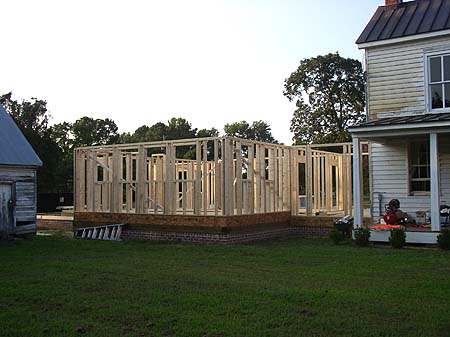
The framing continued today. As did the surprises. Like this kitchen window...
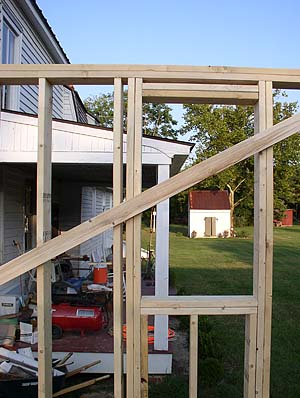
When the back porch is extended over to the new kitchen, the new porch post will land right in front of this window. Not good. Called the architect for a solution.
Meanwhile, we won't see the framing crew again until Monday. -- Bill
Our framing crew was back yesterday as promised, but by the end of the day I was so frustrated and stressed that I couldn't bring myself to relive the day by posting an update to the journal. That's the first time that that has happened to me in six years!
The new center hall staircase has been a bear ever since we decided that we wanted to use the double doors that we found in the chicken house. These doors are 7'-4" tall. This, combined with the shallow depth of the hall, makes it nearly impossible to get the stair landing high enough to clear the rear doors. Admittedly, this was a monkey wrench that we threw into the plans when we discovered the doors, but our architect assured us that it would work "beautifully." Long story short, it didn't. Yesterday we had to put the plans aside and basically design a solution on site. The solution involves giving up one of two planned doors into the dining room from the hall. And even so, I'm not completely sure that our solution meets code. I need to make a phone call tomorrow.
There have also been small errors that have snowballed into larger problems. Like two kitchen windows placed exactly 30 inches apart in order to accommodate a 30" wall oven between them. Well, a 30" wall oven needs to be housed in a cabinet. A cabinet that is 33" inches wide. When I spotted the issue (always running around with my tape measure...) I discussed it with the lead carpenter and asked that they simply move one of the windows to the left to accommodate the oven cabinet. That was last Thursday. I reminded him again yesterday and this morning when it still hadn't been moved. Then I left for two hours and upon my return found that they had sheathed the wall without moving the window, so now the sheathing has to be torn off so they can move the window. Oy.
I think we have resolved the porch post vs. window issue. The solution's not great, but it's the best the carpenter and I could come up with. All of the possible solutions had domino effects that were worse than our solution. I asked for the architect's help with this last week, but I haven't heard anything back from him yet and we had to keep things moving.
I think a lot of the problems we have run into are a fact of life with hand drawn plans. I gotta respect the lost art of hand-drawn plans, but I'm also becoming intuned to the pitfalls. Human error in transferring dimensions being a biggie. Also, our revision requests have created a nightmare. After our architect completed the "final" drawings, we decided that the width of the center hall just wasn't wide enough. The hall was originally 8 feet wide and we increased it to 10 feet. And we decided that instead of moving the windows in our already-restored dining room in order to create symmetry on the front of the house, that we wanted to move the windows in the law office instead. Because revising the entire set of hand-drawn plans would have been hugely time consuming, we received a revision page which only addressed the center hall and the windows. The trouble is that this requires that everybody on the job constantly be reminded that if you're dealing with the center hall and windows, you need to refer to "this sheet." For anything else, refer to "that sheet." This has resulted in a fair amount of confusion on the job site and in window openings having to be moved after they were framed. It's easy for the framers to get into a groove, working away, and forget that they need to refer to the other page for something.
I think the post-in-the-window incident probably could have also been prevented with CAD. The original plans included a one-foot scaling error in the kitchen. When we discovered this on site I asked the architect to revisit the kitchen and give me revised locations for the windows, etc. Instead of redrawing the kitchen, he sent me the same drawing with revised dimensions written in. Because the kitchen wasn't redrawn, nobody saw that the new dimensions put the window behind the post.
OK...enough of this. Nothing has yet to be insurmountable and probably it's all just par for the course. But that doesn't make it any less frustrating when it's happening.
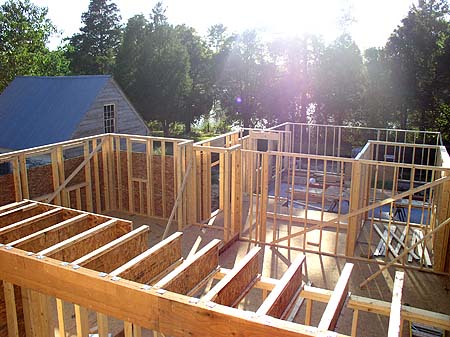
Here's the view from William's bedroom door late this afternoon. Despite some stumbles, there's lots of progress being made. -- Bill
Today wasn't a day of dramatically visible progress...but there was a lot of heavy lifting going on as the crew wrestled beams and headers into place to get ready to start installing the second floor joists. Tomorrow they will be off on another job and then return here on Friday. -- Bill
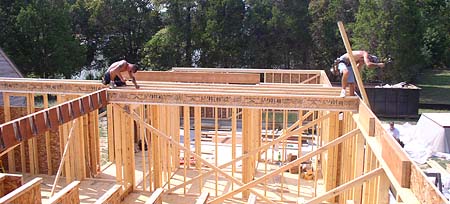
Today the second floor joists started going up. Or as the locals call them, "joistes." The long-floating law office door will soon be functional again as William's bedroom door.
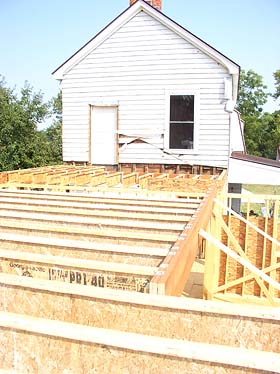
The question of the day..."How are you going to park your car in the garage with this post in the way?" Sure enough, unless we're all reading the framing plan wrong, there's a pipe column sitting right where I hope to someday park my car, carrying the end of a beam that spans the garage. Easily remedied...with more money. I ordered longer, thicker (and more expensive) LVL beams to span the full distance, eliminating the need for the column.
Today I met with a plaster contractor and an insulation contractor. I'm excited about the blueboard plaster veneer system and hope that the pricing works in our budget.
Speaking of which...
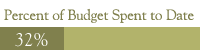
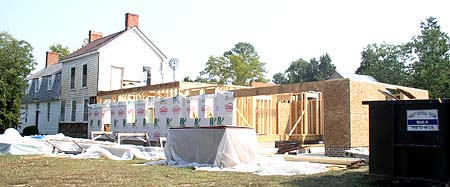
Also got clearance on the center hall staircase from the building inspector. (Thought that would be good to do before we actually built it.) -- Bill
We have subfloor upstairs now!
I provided the framers with a good laugh this morning. I was leaning on a window opening with my feet crossed, chatting with two guys inside and one outside. Then another guy approached with a sheet of plywood, getting ready to hoist it up to still another framer on the second floor. I went to step aside, but to my surprise I just spun around like a ballerina and fell like a rock to the ground. What the heck?! Turns out that when I had crossed my feet the loop on the back of my right boot had gotten hung on a shoelace hook on my left boot...essentially tying my boots together quite securely. With five witnesses on hand. Oh well...when the laughter subsided it led to lots of good stories from everybody else.
I travelled many a mile today to visit a home where the blueboard plaster contractor I am talking to was supposed to be working today. Long story short. He wasn't there. But man, what a house it was! An early 1800s Dutch Colonial being restored to the nth degree with obviously no shortage of financial resources. At least I got to see the prep in the room. One of the things that I really like about this system is that you can put all of your wood trim up first and then plaster to the trim. A much more authentic look. Of course all of the moulding needs to be thicker. Ka-ching. -- Bill
Today the crew focused on battening down the hatches for our expected rainstorm from Ophelia. We haven't had a drop of rain since the framing crew started on August 15th, and I can't remember how long it had been before that even. So I guess we're due, even though the dry weather has been great for making progress.
The gable end of the 19th century addition already had a lot of siding removed, so they went ahead and removed the rest of it up to the top of the law office door and window.
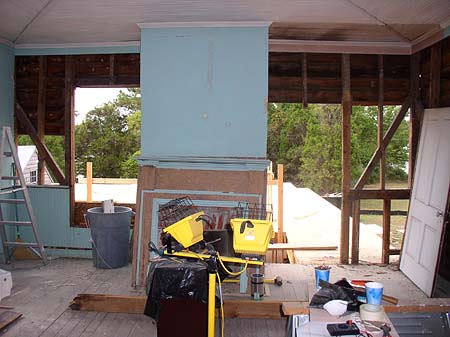
Then they sheathed over everything with 5/8ths plywood. They'll come back later and fill in the framing where the window was and re-frame the door opening since it is having to move to make the staircase work.
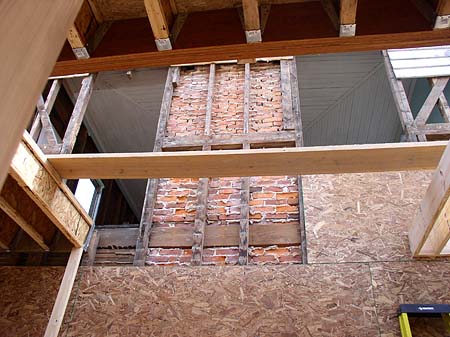
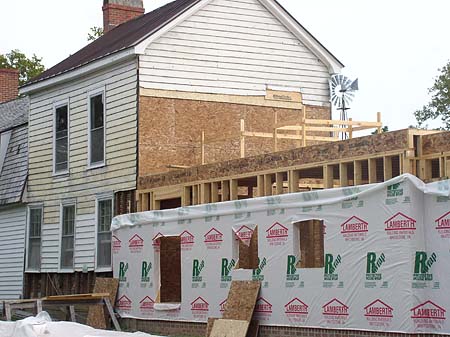
Even though this is becoming an interior wall, I requested that we sheath it under the blueboard to stiffen everything up and prevent any future racking.
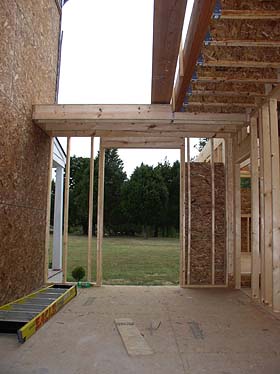
Here's the new center hall from the front door. The staircase will run up the left wall to the landing and then there will be one more step up to second floor level.
I think it's exciting when things arrive in crates!
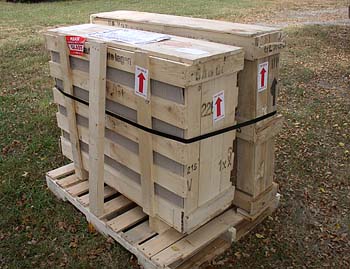
The new wavy window glass for the addition windows arrived today. William has already called dibs on the crates...for...something... -- Bill
Well, we never did get a drop of rain so we got in two more work days. Things are really coming along nicely. The walls are about 80% done upstairs and the stretchers are in for the new center hall staircase.
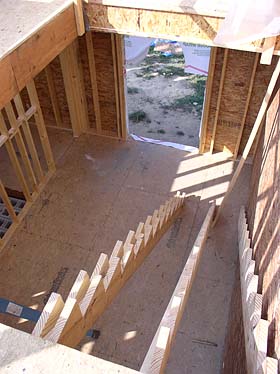
My code question last week had to do with whether our bottom stair would be far enough back from the front wall. The answer was that this space is treated like a landing and, as such, needs to be as deep as the stairs are wide. We were able to meet that requirement, plus 3 inches so we're in good shape. And since the front door is a double door, each being just 24" wide, we have plenty of clearance for the door swing too.
Once the upstairs walls were chalked out on the subfloor yesterday, we decided that we weren't going to have much room between the end of our bed and the fireplace hearth. As one of the framers said, "I hope you don't kick your covers off in the middle of the night." We decided we could afford to steal a foot from the walk-in closet, so all is well. It's great to be able to make decisions like that at the chalk stage.
I'm excited about a new idea. We planned for a laundry chute that drops from our walk-in closet to the laundry room directly below. Well, now we're investigating a dumb waiter for the same purpose, so not only could dirty laundry go down, but clean, folded laundry could come right back up to the closet! The very first price I got back is for an electric dumb waiter and it runs about $2,500 for the kit. I'm going to check into manual waiters too. It's not cheap...but, wow...what a cool, labor saver that would be if we can work it into the budget!
I've been very happy with how neat our framing crew has kept the work site. They clean up every day and chuck everything in the dumpster. And we've been successful in keeping all the stacks of lumber, cars, trucks, etc in the front yard so that the creek side of the house is pretty untainted. Makes it much easier to live through.
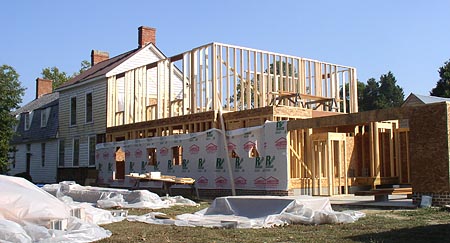
It's been 4 weeks now since the framers arrived on the job. They've been here every day except three with a crew ranging from 3 to 9...usually 4. They've made an amazing amount of progress for such a short period of time. Certainly going faster than the foundation did!! -- Bill
Framing is progressing nicely. Now the floor joists for the room above the garage are in and most of the upstairs walls are complete.
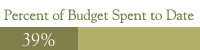
The budget is starting to be spent at a more rapid rate. The next 30 days will probably be the most expensive of the whole process, then I expect things will slow down a little. Mentally, I'm gonna hate it when we hit 50%...signifying that the glass will then be more than half empty. (Or less than half full for the optimists.)
After the crew left today we got our first rain since framing began...and boy, it's a gully washer! Hopefully, it will pass and we'll be back in business tomorrow. -- Bill
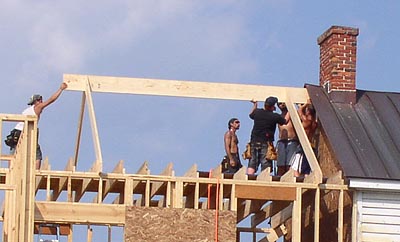
The ridge board and first new rafters went into place today as the addition finally reached the top! This represents another critical mile marker in tying in to the old part of the house. Both floors meet up nicely with the old, and now so does the roof.

Gay was checking out the view from one of the two master bath windows. After she stopped exclaiming, "The shower is huuuuuge." Hey, I asked our architect for a big shower and that's what he drew. It's 6'X4' inside. It's not that I'm a big guy...but I spent years taking showers in tubs with the shower curtain sucked to me, so I'm making up for lost time.
Yesterday I picked up our honkin' new window sills from the millwork shop. These match the dining room sills and are 4-5/8" thick at the back. I had them made from Spanish Cedar, so they should last as long as the house. Today I primed them and tried one on for size.
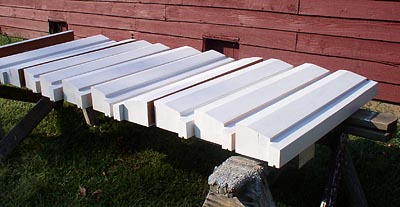

A perfect fit! -- Bill
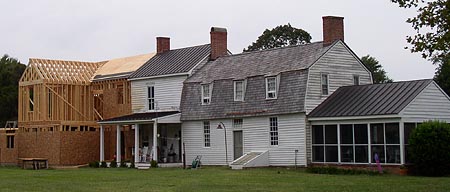
Two areas of the new roof rafters are in and the plywood sheathing and tar paper is beginning to go down. Our roofer is on standby to get going with the copper as soon as the sheathing is all down and the cornices have been trimmed. Our mason is due back this week to work on the fireplaces and chimney and the porch piers.
I spent the morning putting together a list of all of the moulding that I will need to trim out the doors and windows. This is one area where I'm finding that I will probably go over my budget. Replicating the trim in the original part of the house is important, but pricey. Also determined the profiles for the sills for the new front and back doors. Another trip to the millwork shop is now in order.
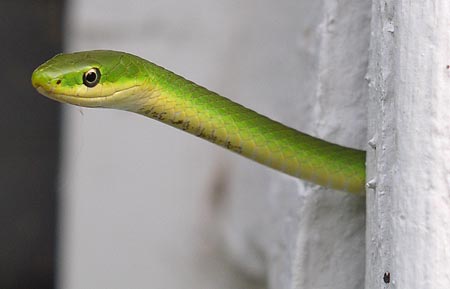
This little fella spent most of the afternoon with his head sticking out from a crack around a piece of corner trim. He seemed to be quietly enjoying the day. -- Bill
Our little snake was back today, sticking his head out of the same crack for most of the morning. Wonder what he's up to...
Our mason was back on the job and today dug and poured the footing for the front porch and for a new pier for the back porch.
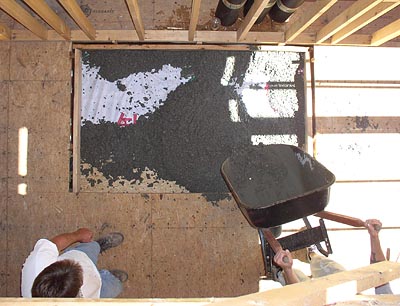
They also poured a 4-inch pad on top of the chimney foundation to support the hearth and firebox.
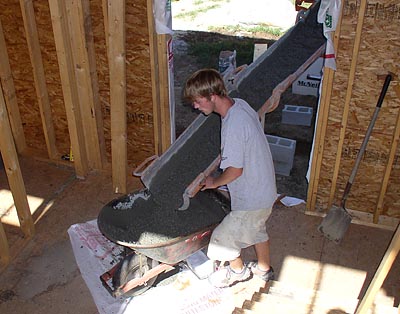
It's more than a little disconcerting to have the chute from a cement truck sticking in your front door pumping concrete into a wheelbarrow. My discomfort was well founded when seconds after I took this photo the wheelbarrow capsized, dumping the full load onto the subfloor. I spared the mason's assistant the humiliation of documenting that with a photo. They got it all cleaned up with no lasting effect, other than the psychological damage done to the assistant by the cussing of his boss.
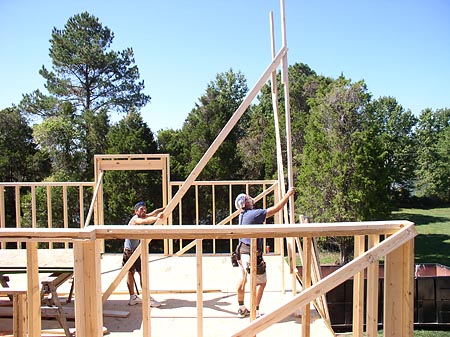
The erection of these goalposts above the garage had me a little puzzled. And when the only explanation I could get was "We're gonna play football at lunch," I had to figure it out myself. Turns out these will support the ridge board while the rafters are put into place. Then the collar ties will go across the rafters, creating the ceiling for this room.
We keep finding artwork here and there, sketched out on the sides of studs, etc. This afternoon I looked up into the attic space and saw a board nailed to the very top of the gable. With the assistance of a ladder and the camera's zoom, I was finally able to make out the art.
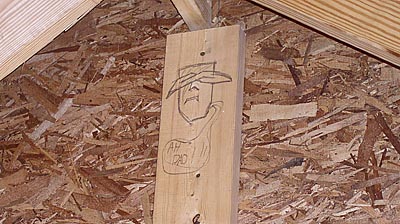
One of the young framers calls the 52-year-old foreman "Dad." And when the foreman gives him a mission that he doesn't particularly relish, we often hear him exclaim, "Aw, Dad!" I assume that this is his handiwork. Made me chuckle. We'll keep it there for others to try to figure out the meaning of years from now.
Ordered a limestone tread for our front porch step. I'm excited aboout that...always loved them. Should be here early next week. -- Bill
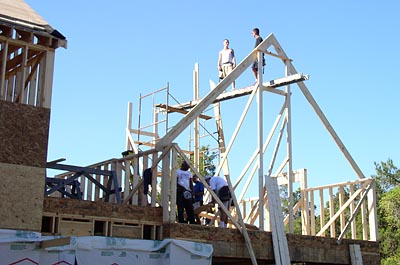
We saw the goalposts put to use today, although not exactly in the way that I had predicted. The goalposts were part of the scaffolding system.

We've decided to raise the ceiling height in the room above the garage from 8 feet to 10 feet. Yeah, I know...more expensive to heat and cool. Oh well.
The other part of the roof is now dried in with 30-pound felt paper.
I'm exploring slate for the colonnade floor. We really want the look of irregular patio slate, but I can't find it in 3/8 thickness...only square and rectangular tiles. I'm halfway considering ordering large 3/8 thick slate tiles and then breaking them into irregular shapes. But it would be quite a job to get rid of all of the straight factory sides. Not to mention the waste involved. -- Bill
|